The manufacturing industry comprises heavy investment plant assets that need to be closely monitored to deliver optimal performance. In such industries, lack of proper maintenance has a negative impact on overall operations, and profitability– leading to higher downtime, increased maintenance costs, and reduced asset lifespan.
Implementing plant asset management helps deal with aging machinery and can lower equipment downtime by 20.1%. This can be achieved by having a dedicated system to govern manufacturing plant assets throughout their lifecycle.
This article takes you through the basics of plant assets, challenges and benefits of manufacturing asset management.
What is a plant asset?
A plant asset is usually a fixed asset such as property, or equipment that is expected to be utilized for the long term. To ensure maximum returns on plant assets, it is critical to manage them using the right tools properly. With the correct management strategies, manufacturing companies can prolong the life of their plant assets to achieve peak performance. Here are some examples of plant assets:
Machinery and equipment: This includes all types of heavy-duty assets used in the manufacturing process, such as milling machines, drills, and conveyor belts.
Property: Refers to buildings, land, factories, and warehouses owned by the company.
Vehicles: All transportation including trucks, bulldozers, and vans.
Key components of plant asset management
Plant asset management primarily consists of services, software, and hardware deployed by a manufacturing company to monitor assets over their lifecycle. This usually includes tracking equipment, parts, and production lines to ensure everything is working to its total capacity. Let’s briefly look at the key aspects of manufacturing asset management:
Asset and inventory tracking: Keeping an updated asset register enables you to track stock quantities, availability status, and condition using RFID tags or barcodes.
Proactive maintenance: Plant assets require timely inspections and service for uninterrupted performance. Preventive maintenance can be scheduled to minimize unexpected downtime.
Lifecycle management: Accurate records enable seamless asset depreciation calculations. Using these estimates, manufacturing companies can make informed decisions about item replacement, upgrade, and refurbishment.
Regulatory compliance: Different types of plant assets have various standard and quality requirements that must be met to ensure smooth equipment operation throughout projects.
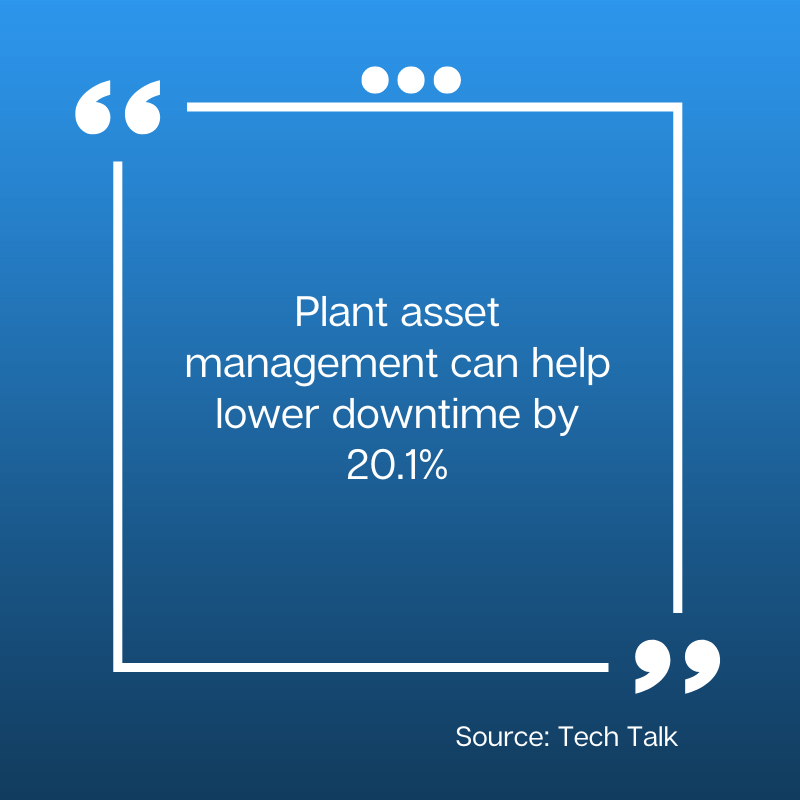
4 Common challenges in managing plant assets
To design an effective plant asset management system for your company, it is vital to understand the common challenges in the manufacturing industry:
Lack of data interpretation tools
The manufacturing industry is rapidly digitizing. With online management systems, companies make great efforts to record maintenance costs, usage times, and labor hours. However, most manufacturing companies are not equipped with the right tools to interpret primary data into actionable practices. This results in large volumes of information being wasted with suboptimal asset utilization.
Inventory mismanagement
Manufacturing companies often deal with turbulent customer demand. For instance, to cater to increasing demand, plant capacity has to be increased. Without a robust management mechanism, manufacturing facilities fail to fulfill inventory requirements, thus missing out on potential clients and revenue.
Aging infrastructure
It is common for manufacturing firms to rely on aging infrastructure or those nearing the end of their life for operations. The average useful lifespan of machinery and equipment in the manufacturing industry is around 10-20 years. Extending the use of assets beyond this time can lead to frequent downtimes, failure rates, and the inability to find spare parts due to older models.
Cybersecurity threats
The number of ransomware incidents in the manufacturing sector has increased due to security lapses in the adoption of cloud platforms without attention to data protection practices. Manufacturing companies must invest in the right technology to combat security breaches and protect their data.
5 Benefits of deploying automated plant asset management
An automated asset management system for your manufacturing plant offers a variety of features to help optimize the production processes. Let’s briefly discuss the top benefits of plant asset management for your company:
1. Compliance with rigorous safety requirements
Manufacturing processes involve daily exposure to heavy machinery and equipment. Without the proper safety mechanisms in place, accidents can happen. From 2019 to 2022, the manufacturing sector experienced over 10,000 Occupational Safety and Health Hazard Administration (OSHA) violations, resulting in penalties worth $38 million.
Complying with safety standards is necessary to avoid hefty violations. A cloud-based plant asset management system enables manufacturing companies to run regular equipment inspections to lower breakdown instances. With every machine tagged in the system, technicians can easily check when inspections are due. For ease of use, managers can attach safety requirements along with equipment details so that all regulatory details are followed.
2. Cater to fluctuating costs
Manufacturing companies face uncertain cost fluctuations due to the number of variables involved in the process. These include factors like demand, labor, raw materials, and the cost of certification and testing. To streamline production at the plant, it is critical to forecast such changes and alter capacity according to the current price levels.
By tracking purchase orders, admin managers can keep a record of raw material prices while work order forms specify all maintenance expenses. An asset tracking system enables you to record primary data that can be translated into actionable insights.
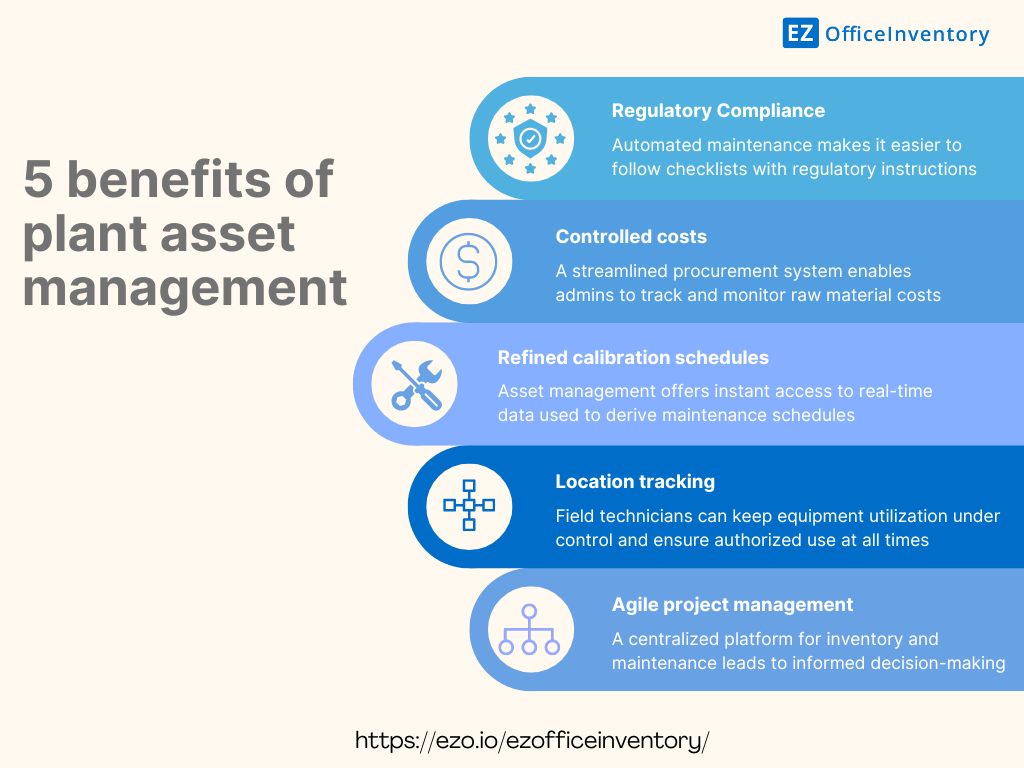
3. Refine calibration schedules
Manufacturing plants use multiple types of machines and equipment to run their production process. Without a certified service checklist, there are high chances of unpredicted breakdowns. To minimize the chances of unplanned downtime, it is vital to establish a calibration strategy that combines real-time monitoring and predictive analysis.
The best way to combat unexpected breakdowns is to inspect equipment and machines closely on a regular basis. This can only be done when you have clear visibility of the tools and assets available at the site. Manufacturing asset management automation offers instant access to real-time data that can then be used to derive maintenance schedules. You can also keep track of equipment performance through service history and maintenance logs. With the right tools, your manufacturing plant can run the correct maintenance routines to lower downtime.
4. Track locations for efficient equipment use
The majority of manufacturing facilities operate across various locations. In such cases, it is extremely important to track each piece of machinery. Failure to monitor mobile equipment can increase theft and misplacement at the production site.
A plant asset management system enables companies to track every location where machines are being used. Real-time location tracking enables field technicians to keep equipment utilization under control and confirm that it stays with authorized personnel. The ability to track locations also ensures that the machinery is handled within the safety limits for production at the plant.
5. Practice agile project management
Successful project completion requires manufacturing plants to adhere to strict deadlines set by clients. However, working with outdated tools can hold your company back and eventually lead to revenue and profit loss. A critical part of lean project management involves having clear visibility of the availability of staff and equipment. When you know about your inventory, you can make delivery commitments without inconvenience.
A robust asset management tool allows the company to view the status of all equipment owned by the company on a centralized platform. Quick access to inventory levels and maintenance schedules leads to informed decision-making and promising production outcomes.
Automate plant asset management for seamless operational performance
A reliable system to manage plant assets focuses on data accuracy, lifecycle tracking, and compliance regulation to lower downtime. With the right tools, manufacturing companies can set up proactive maintenance to cut down unnecessary costs and track locations to control plant assets across warehouses. In this way, structured plant asset tracking ensures optimal equipment utilization with a prolonged useful life.