Put yourself in the shoes of a facility manager (let’s say, Frank) at a busy downtown office building in New York. Being a facility manager, we are certain he knows the drill all too well. The tenants of the building are demanding. Plus, the budget cuts are looming and the outdated and aging HVAC system is on its last leg. We’re sure this rings a bell for him.
In today’s ever-challenging environment, keeping a building running smoothly while managing costs can feel like a super-hero task. Frank is often praised for his job when everything runs smoothly within the building. However, he is suddenly put on the spot if something goes wrong. Suddenly, he is being blamed for everything related to the facility management.
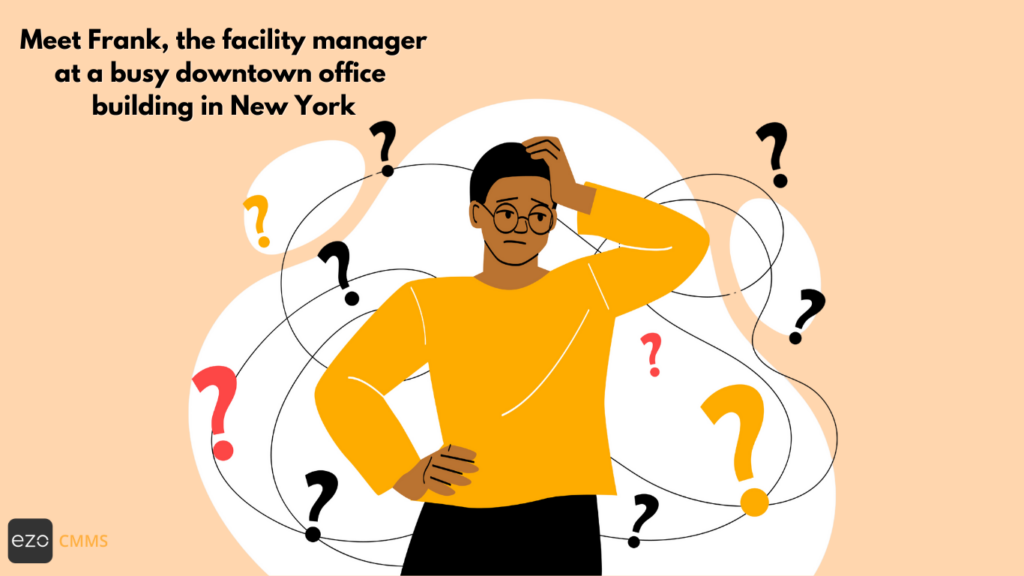
He is constantly under pressure to reduce facility maintenance costs. He needs to demonstrate the value of his work. It’s hard when the general narrative is that his team is merely a “cost center/complaint department”, not one that’s critical to business success.
For instance, he is to blame if the HVAC system in his building fails to operate correctly or suddenly breaks down. His HVAC maintenance technician confirms that it is a significant issue that will cost a lot of money and take several weeks to repair.
On the other hand, his renters started demanding a full refund for the period they could not use the space due to an HVAC breakdown.
That being said, he could have prevented this issue had he and his maintenance team performed a routine maintenance inspection on time and caught the problem before it got worse. Proactive maintenance, rather than reactive maintenance, would have done the work here.
Cost implications of building maintenance
Building maintenance can be costly and challenging to manage.
Equipment maintenance has long been seen as one of the most significant operational expenses in facilities management, often making up around 15 to 18 percent of a building’s total operational budget.
Maintenance costs are estimated to range between 15% and 40% of total production costs.
According to the U.S. Department of Energy, organizations spend nearly $50 billion every year on industrial equipment maintenance, with a major portion of that budget being consumed by unexpected repairs and inefficient management practices.
Additionally, a study by McKinsey & Company revealed that companies that adopt a predictive maintenance strategy can reduce their overall equipment maintenance costs from 10 to 40%.
Without a proper preventive maintenance plan, a major infrastructure failure can happen out of nowhere, costing your company thousands of dollars in repairs and leaving your building closed for months.
The key to reducing the maintenance costs in your building lies in leveraging modern technology and AI-powered maintenance solutions — real-time data and analytics — to simplify your maintenance operations and make smarter, data-driven decisions.
This article discusses 10 simple ways facility managers like Frank can implement to reduce costs, save money, improve building efficiency, and keep tenants happy.
10 Ways to Reduce Building Maintenance Costs
Building management involves maintaining and overseeing the physical infrastructure of a building. Let’s explore some of the simple yet effective ways to reduce building maintenance costs:
1. Implement a preventive maintenance program
Regularly performing scheduled maintenance can prevent your equipment from costly breakdowns and extend its lifespan. You can think of preventive maintenance as your building’s regular check-up. It is about performing regular inspections and servicing your equipment rather than waiting for it to break down first and face a costly emergency repair.
As facilities managers, it is crucial for you to understand the importance of preventive maintenance. Following a proper plan, you can schedule regular filter changes for the building’s HVAC system without waiting to hear complaints from the tenants or for it to break down.
Another tip would be to regularly check the pumping system to ensure there are no water leakages before they become major water damage issues. These proactive measures not only increase the lifespan of the equipment but also improve energy efficiency and reduce disruptions.
2. Educate your staff
Another best approach to reduce maintenance costs in your building is to educate your staff. It is important to ensure that your staff is adequately trained on using and maintaining the building equipment. This can reduce the risk of damage and misuse, leading to fewer repairs.
When you invest in training and empowering your maintenance team, you can address minor issues before they become major ones.
As a facility manager, be sure to regularly hold training sessions with your team and educate them on equipment maintenance and tenant communication.
Also encourage them to report any potential issue they face while performing their daily tasks, empowering them to take ownership of the upkeep of the building.
3. Leverage advanced technology
Have you ever wondered what it would be like to adopt advanced software and tools to help streamline your maintenance processes like scheduling preventive maintenance, creating work orders, or tracking inventory?
These smart tools can help you reduce maintenance costs. In today’s digital age, consider technology as your ally. A computerized maintenance management system (CMMS) can simplify challenging maintenance operations, leading to cost savings and operational efficiency. The battle for the best CMMS solution is never-ending – MaintainX vs UpKeep vs EZO CMMS. You need to pick the best one!
Consider Frank recently coming across a great CMMS solution and pushing for its implementation so his company can get rid of its current manual system and spreadsheets. That’s the best way to maintain your equipment!
He envisions using maintenance management software to automate work order requests from tenants, schedule preventive maintenance tasks, and track inventory of frequently used parts. An advanced CMMS solution, with a complete set of key CMMS features, would help free up his time so he can focus on what needs the most attention – strategic maintenance planning and cost-saving initiatives so that he can position his department as one that’s not just a cost center but one that’s critical for the business success of all tenants.
4. Focus on energy efficiency
Sustainability is not only being used as a buzzword these days–it’s a smart financial strategy for organizations. Using energy-efficient materials and implementing eco-friendly practices can significantly impact your bottom line. It reduces your utility bills, wear and tear on your equipment, and, eventually, your maintenance costs.
One of the key examples of adopting sustainable practices in your building would be going for LED lights to save on energy costs. You can consider different options for upgrading the building’s lighting to LED fixtures.
This will not only contribute to reducing energy consumption and utility bills but also improve the building’s overall appearance, which can help attract environmentally conscious tenants. Besides that, you can also consider using smart thermostats to optimize energy usage based on occupancy.
5. Negotiate with vendors
It is essential to review your contracts with vendors and service providers regularly. Negotiating better prices with your suppliers for maintenance services and materials and maintaining strong relationships with your vendors can save costs. Next time, you get to work with a vendor, try exploring competitive bids and negotiating pricing based on volume or long-term agreements.
In Frank’s case, he would be interested in reviewing their contract with the repair and cleaning company. He can actively compare bids from other service providers and suppliers and leverage their long-term relationship to negotiate a better price.
6. Stock up inventory smartly
One of the effective ways to reduce downtime and maintenance costs is to stock up spare parts inventory smartly. Though it is crucial to avoid overstocking spare parts at a high price, you must ensure you have the necessary items to keep the downtime to a minimum.
Proper equipment maintenance tracking lets you track which spare parts are used more frequently for repairs and need replacement more than often. You can ensure you have the right parts available when you need them, preventing unnecessary delays and overstocking parts that can lead to higher maintenance costs.
With inventory forecasting, Frank can handle his job exceptionally well because he analyzes his inventory of frequently used parts like HVAC filters, plumbing fittings, etc. He also identifies items used more frequently and negotiates bulk discounts for them with their vendors.
7. Make repairs a priority
In a maintenance department, you come across multiple requests for repairs. However, not all of them should be given priority. There should be a system in place that helps you prioritize work orders based on urgency and potential impact. Critical repairs should be prioritized, especially those directly impacting operations or safety, to prevent further damage and costly downtime. Effective asset maintenance helps you prevent costly repairs.
As a facility manager, you can set a system in place where you categorize tenant requests based on urgency. For instance, if there’s an emergency repair like an HVAC breakdown or pipe burst, then these repairs should be prioritized immediately.
Less urgent repairs like flickering lights can be scheduled for later. This can allow you to allocate resources effectively in the building, preventing minor issues from becoming bigger problems.
8. Perform regular inspections
Performing routine inspections is also one of the key ways to reduce maintenance costs in your building. You can identify potential issues early on when you conduct routine inspections, preventing them from escalating into major, cost-heavy repairs. This can help you save money in the long run and cut down on your maintenance costs.
You can do a fantastic job at performing routine inspections of the building’s most-used areas, including hallways, lobby, and restrooms.
You can also check the building’s critical systems, like the emergency generator and the fire alarm system, to ensure they are working properly. You can prevent fire incidents by ensuring your facilities are more fire-resistant. A pro tip is to create checklists for these inspections and use them proactively to ensure nothing is overlooked.
9. Invest in high-quality materials
Let’s just admit that it is quite tempting to opt for materials and equipment that are cheaper. However, you may end up incurring more costs if you opt for cheaper materials and equipment. Investing in durable, high-quality materials for repairs and replacements may be a little costly, but it definitely pays off in the long run.
Frank realizes that opting for durable, high-quality plumping or HVAC components for the building, even if they come with a higher upfront cost, will reduce the need for frequent repairs and replacements in the future, helping them save money in the long run.
10. Outsource when necessary
You can consider outsourcing to qualified professionals when you lack in-house expertise or want to get done any specialized tasks. This ensures quality in your work and prevents you from making costly mistakes.
If you’re a facilities manager like Frank who’s skilled in HVAC but only has limited experience with complex electrical work.
When the building needs a major upgrade for installing new electrical panels, it’s time to seek help from the experts.
While outsourcing this task to a qualified professional may have incurred a cost, it can prevent potentially dangerous and costly consequences for using unqualified internal staff members for such critical tasks.
By outsourcing, you can make your team focus on their core competencies.
Reducing Costs, Building a Better Bottom Line
Proper upkeep of your building to ensure it remains fully functional and the occupants are safe and comfortable is essential. You should not let your critical maintenance tasks slip through the cracks.
It is worth mentioning that reducing your building maintenance costs is not a one-time effort – it’s a continuous process. However, by implementing these 10 simple strategies, facility managers like Frank (and you) can significantly improve their building’s bottom line. Not only that, but you can also reduce maintenance costs in your building without having to sacrifice safety or quality.
Keep building maintenance EZ with EZO CMMS! 🙌