While at work, relying completely on luck or hoping for spare parts to be in stock is not a strategy for success. Running maintenance operations effectively is all about addressing such challenges head-on.
According to the Plant Engineering 2020 survey, 18% of companies spend 40 hours or more per week on maintenance tasks.
So when investing significant time in maintenance, you must ensure that all operations are carried out smoothly.
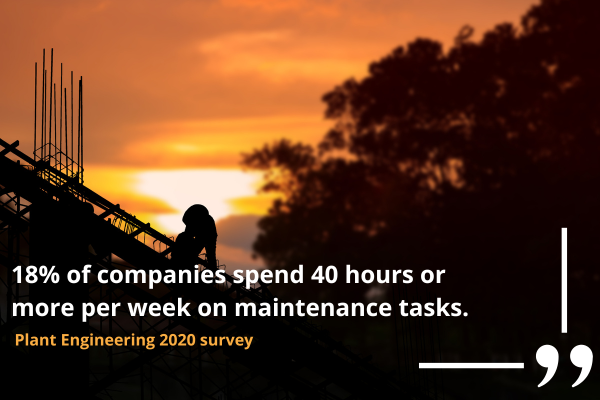
While some issues are unavoidable, many arise from poor maintenance of equipment. Proper maintenance of every asset, whether they are used within a manufacturing facility or a service company, can be streamlined and expedited through EZO CMMS – the next-generation computerized maintenance management (CMMS) software. For a restaurant business, restaurant equipment maintenance is necessary and this is only possible with a robust CMMS solution.
Results from Plant Engineering’s Purchasing Considerations for Maintenance Management Software survey indicate that about 59% of those surveyed said they use a CMMS system as their maintenance software.
Consider the challenges your maintenance teams have to face every day – frequent equipment breakdowns, backlog, shortage of parts, budget overruns, and much more. Luckily, EZO CMMS software offers an effective solution for maintenance managers and technicians to overcome all these maintenance issues.
The best part about using EZO CMMS software is that you do not have to rely on several tools to complete your job. It is a robust all-in-one solution for all your maintenance needs, solving 90% of your problems at their core.
Why EZO CMMS is important for your business
EZO CMMS is designed to enhance the productivity and efficiency of an organization’s operations and processes, leading to reduced costs and increased return on investment.
Using EZO CMMS allows businesses to strategically plan and manage their operations, allocating the right resources to meet their objectives. Through key features such as detailed reports and maintenance key performance indicators (KPIs), EZO CMMS provides businesses with complete visibility into their maintenance operations.
Furthermore, EZO CMMS automates workflows and maintenance tasks, leading to reduced downtime and improved efficiency. Its implementation can also enhance decision-making and task execution across the company. For example, the reports collected and generated by our CMMS software help businesses make better and more informed decisions about which maintenance strategies need to be implemented.
Top 5 EZO CMMS features every business should use
Let’s thoroughly discuss the top 5 EZO CMMS features that can alleviate your maintenance problems.
- Work order management
- Scheduled maintenance planner
- Inventory management
- Instant reporting
- Mobile app
Work order management
EZO CMMS software simplifies work order management by allowing you to create, assign, complete, and record digital work orders and work requests with the help of a few features which are mentioned below:
- Work request portal: You can enable staff outside of the maintenance department to create and monitor work requests with the help of customized request forms, thus improving communication and efficiency and enhancing work request management.
- Asset hierarchy: You can look for assets or asset stock and then associate maintenance work orders with them, facilitating targeted maintenance and asset management.
- Instructions and documents: You can add manuals, photos, task lists, etc. to your work orders, improving task comprehension and completion.
- Parts and safety equipment: You can list all necessary spare parts and safety equipment required for the job, ensuring resources are readily available for maintenance tasks.
- Failure codes: You can create an outline for a problem, cause, and action for equipment failure, facilitating problem identification and resolution.
- Logistical information: You can set deadlines, choose priority levels, and assign technicians for a particular task, ensuring timely and effective maintenance operations.
- Notes: You can add additional details for tasks such as machine sounds before breakdowns for comprehensive maintenance records and troubleshooting.
- Tracking: You can monitor the status of tasks and their costs and then archive completed work orders for effective performance evaluation.
With the help of work order management, maintenance teams can address three major challenges:
Downtime: Streamlining work order processes can significantly reduce equipment downtime.
Inefficiency: With efficient work order management, you can instantly document, submit, and gain access to work requests, reducing operational inefficiency.
Lack of information: Work order management ensures all task details are easily accessible, leading to standard results, improved decision-making, and easier maintenance troubleshooting.
Scheduled maintenance planner
According to Plant Engineering 2020’s report, 76% of manufacturing companies prioritized preventive maintenance.
EZO CMMS software offers a scheduled maintenance planner that simplifies maintenance scheduling with features such as:
- PM triggers: Preventive maintenance triggers work for scheduled tasks based on time, usage, condition, or events; ensuring maintenance is performed on time to prevent equipment failures.
- Calendar: It displays everyone’s schedules, enabling you to assign tasks based on their workload.
- Maintenance forecaster: It enables you to match upcoming tasks with inventory purchases and work schedules, ensuring the availability of resources and timely task completion.
- Inspection checklist: You can attach a list of inspection tasks along with pass/fail guidelines, ensuring thorough inspections and compliance with maintenance standards.
- Scheduled maintenance metrics: You can track metrics such as planned maintenance compliance for better performance evaluation and continuous improvement.
- Integration with work order management: You can add comprehensive details available for a work order to a scheduled maintenance task, ensuring clarity and alignment between maintenance planning and execution.
A scheduled maintenance planner in EZO CMMS resolves the three main challenges:
Reliance on reactive maintenance: You can establish a preventive maintenance program to reduce the number of fires your team puts out daily, enhancing safety and production.
Performing excessive preventive maintenance: With the help of a scheduled maintenance planner, you can avoid performing extensive preventive maintenance and determine the best task frequency to prevent equipment and staff burnout.
Excessive spending: The planner tool provides insights into parts, maintenance workers, and performance metrics to prevent overspending and optimize costs.
Inventory management
Businesses can achieve a notable 10% percent decrease in inventory costs by resolving understocking and overstocking issues.
Inventory management, the notable EZO CMMS feature, enables maintenance teams to manage all inventory aspects, including monitoring inventory levels. Here’s what it does:
- Parts tracking: You can monitor your stock, where it is, and how much it costs. This facilitates efficient inventory management and reduces the risk of stockouts or excess inventory.
- Low stock alerts: You can set minimum and maximum quantities for stock and automatic reordering for critical parts, enabling timely replenishment and preventing production delays.
- First-in, first-out tracking: You can prioritize parts based on the date of purchase, reducing the risk of obsolete inventory and minimizing waste.
- Multi-site visibility: You can access and share parts all across the facilities, promoting centralized control and coordination of inventory levels and purchases.
- Work-associated parts: You can add recommended parts to work orders and preventive maintenance tasks, ensuring the availability of required parts for timely equipment repairs and maintenance.
- Purchasing: You can create, send, and record digital purchase orders, streamlining procurement and improving transparency in inventory purchasing.
Here’s how efficient inventory management helps overcome these challenges:
Disconnected operations: The maintenance teams are not the only ones that require accurate inventory numbers. CMMS software syncs data with financial systems (like ERP) for accurate tracking of maintenance costs.
Increased costs: Spare parts can be costly, especially when inefficient operations affect the purchasing process. Effective inventory management removes these inefficiencies and lowers maintenance costs by forecasting inventory needs and implementing just-in-time delivery.
Inaccessible inventory: The inventory management feature reduces downtime by providing inventory accessibility. It provides the exact location of each part, ensuring easy access and minimizing downtime.
Instant reporting
The one-click reporting feature of the EZO CMMS system streamlines maintenance tracking, analysis, and optimization through these key components:
- Pre-built/custom reports: You can choose from pre-built templates or create your custom reports to get flexibility and efficiency in data analysis.
- Real-time dashboard reports: You can gain instant access to real-time maintenance metrics from your CMMS dashboard, enabling quick decision-making and performance monitoring.
- Automated report scheduling: You can schedule regular reports to automatically run and be emailed to designated recipients, reducing manual effort and ensuring timely distribution of information.
- Financial and audit reporting: You can generate reports for maintenance spending or audit compliance, ensuring transparency, accountability, and adherence to regulatory requirements.
Let’s understand how instant reporting can overcome these significant challenges:
Find the maintenance ROI: The one-click reporting feature streamlines the process of demonstrating the value of maintenance by providing accurate results.
Save time: Automated reports eliminate the need for creating manual reports, saving time for maintenance managers and technicians.
Detect and resolve issues: Instant reporting enables quick analysis and early detection of maintenance issues, leading to prompt fixes.
Mobile app
According to the Software Advice survey, 42% of users identified improved work order tracking as the primary benefit of a CMMS mobile app, followed by 21% who mentioned better decision-making, 20% who reported increased productivity, and 17% who noted reduced asset downtime.
In today’s digital era, maintenance management can be at your fingertips using a mobile CMMS app. Here’s what the mobile app offers:
- QR codes and barcodes: A mobile app helps you instantly access asset details by scanning codes. This facilitates efficient asset management and maintenance tracking without manual entry.
- Push notifications: With the help of a mobile app, you can be notified of new work orders whenever they are assigned to you, ensuring prompt awareness and action on maintenance tasks.
- Asset profiles and work orders: You can access all details of an asset or work order directly from the mobile app, enabling on-the-go task management and decision-making.
- Offline access: You can also enter information into the CMMS even when you’re working offline and have no internet access, ensuring smooth operations.
- Photos: You can take photos from your mobile device and attach them to a particular work order.
A CMMS mobile app helps address these key maintenance issues, anytime, anywhere:
Data inaccuracies: A mobile app reduces errors by enabling quick data input, reducing the lag time significantly between observations and documentation.
Slow emergency response time: Quick access to data within the CMMS mobile app reduces the response time during equipment breakdowns, reducing downtime and enhancing productivity.
Critical working conditions: Maintenance often suffers especially when assets are in different locations or inaccessible. However, the mobile app allows seamless access to information and documentation without frequent trips to the office or being concerned about ruining paperwork.
Optimize maintenance operations with EZO CMMS
Using enhanced tools is the first step toward optimizing your maintenance operations. Despite facing several hurdles that make your extensive to-do list even longer, these five CMMS features can solve around 90% of these challenges.
However, there’s a crucial aspect we haven’t discussed — people. The CMMS features are merely tools that must be utilized properly by people to enhance maintenance operations. When you’re ready to adopt CMMS software for your organization, make sure to invest in proper training and implementation programs to equip your team for long-term success.
There are several CMMS providers out there but EZO CMMS stands out as a leader. It is the next-generation maintenance management software that goes beyond basic maintenance tasks. Not only does it provide your maintenance teams with a centralized command center to assign and fulfill work orders, but it also boosts productivity.
Essentially, EZO CMMS is designed to address maintenance problems, such as equipment downtime, high operational costs, and lack of organization, by streamlining maintenance processes and asset management. All these maintenance challenges can be overcome by employing AI-powered CMMS solution, and EZO CMMS is one of them!
It is most suitable for businesses in manufacturing, facilities management, construction, healthcare, and other industries that rely heavily on equipment maintenance. EZO CMMS, equipped with GPS tracking for heavy equipment, helps these industries improve equipment uptime, lower costs, boost productivity, and ensure regulatory compliance.
Hamza Amin, the Senior Product Manager at EZO CMMS, emphasizes, “The company prioritizes a people-centric, work-first approach to maintenance that goes beyond just creating records for work orders.”
In operations-heavy organizations, he believes equipment maintenance plays a crucial role. Without a proper system to guide them, managing maintenance tasks can become challenging.
“Considering this key challenge, EZO CMMS empowers teams and people to efficiently manage their tasks, and through key insights and advanced item analytics, allows businesses to justify cost reductions and improve efficiency,” he added.
Frequently asked questions
What is the most unique and powerful feature of CMMS?
The most unique and important feature of CMMS is the maintenance scheduling process. This essential feature helps maintenance teams efficiently manage maintenance operations, especially when dealing with multiple assets, ensuring no equipment is missed or overlooked in the maintenance process.
What should I look for in a CMMS?
While choosing CMMS software, it is important to consider key factors such as its features, user-friendliness, security measures, implementation process, customer support, and customizability.
What are the requirements of a CMMS?
When evaluating CMMS software, the most essential functions you need to look for include:
- Asset management
- Work order management
- Preventive maintenance
- Inventory management
- Reporting
- User-friendly mobile app