Manage All Your Work Orders, From One Place
We're Trusted by the Best
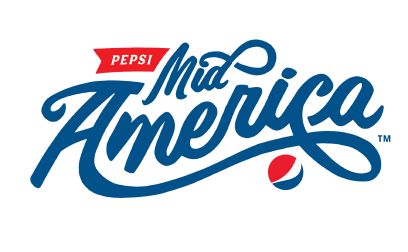
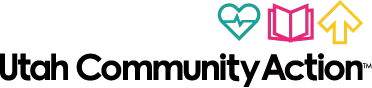
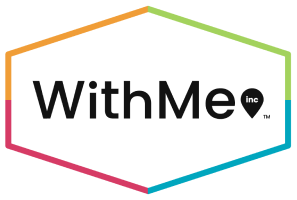
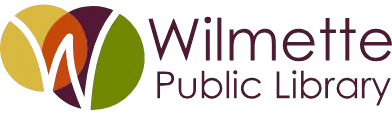
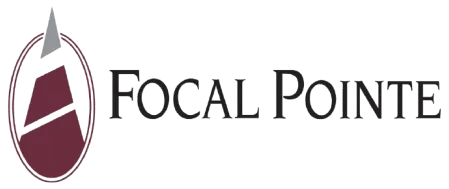
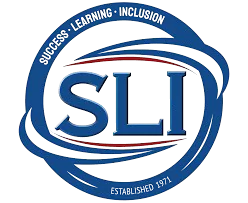
Top Benefits of Work Order Software
Make Maintenance Easy
Are your work requests from different sources piling up? Is maintenance becoming more of a hassle than a problem-solver for you? With EZO CMMS, your requesters can log their maintenance requests on a single platform, making it easier for you to manage them.
Always Stay Updated
A quick update on your maintenance team’s progress is crucial. The comprehensive dashboards and notifications give you a bird’s-eye view of your work order schedules, progress, KPIs, and incurred costs, so you’re up to date on all things maintenance.
Become Error-Free
Manual tracking of work orders with spreadsheets often leads to stress and slows down task progress. Our work order software comes in handy as it reduces human errors in logging work order details, speeds up work order processing, and stores your data in a secure place.
Empower Your Field Teams
As maintenance managers, you need proper coordination with field technicians who work on repairs and inspections on different sites. Mentions in EZO CMMS enable technicians to talk to relevant people by tagging them and coordinating on time.
Let Your Assets Run Longer
With no regular maintenance and inspection, your equipment can lead to major breakdowns before they occur. EZO CMMS, our work order software, lets you schedule regular preventive maintenance to keep your equipment running smoothly.
Your Work Orders, Your Way
Handling work orders when you are working on multiple projects can be challenging. EZO CMMS provides custom fields to help you track information on work orders relevant to your specific project. Custom filters and custom reports help you pull up the right details.
All-in-One Work Order Software for Every Need
Work Order Management
Automations
Offline Mobile App
Public Request Portal
Checklists
Work Order Management
Stay in Control of Work from Start to End
Monitoring the status of your work orders from start to finish is key for efficiency and better communication. Whether you’re running a large retail store with multiple outlets in different locations or keeping track of repairs on a small school campus, EZO CMMS keeps you informed about the progress of each work order. With complete visibility into all work orders, quickly find out about the delays on time and make sure maintenance tasks run without any interruptions.Automations
Prioritize Work Orders, Minimize Delays
It is easy to get overwhelmed with tasks when your team picks up every work order. As a facility manager, you can prioritize critical work requests over routine scheduled repairs. With our advanced work order software, you can automatically assign high-priority and emergency work orders to technicians by creating automated workflows. For instance, a healthcare facility may need to quickly repair a faulty ECG machine to ensure patients receive uninterrupted diagnosis and quality care.Offline Mobile App
Keep Tasks on Track, Internet or Not
Are your field technicians facing difficulties completing their work orders in areas without internet connection? The offline mobile app feature in our work order software allows them to view work orders assigned to them offline, where they can add work logs. The app seamlessly switches between online and offline modes based on the availability of the internet connection, allowing technicians to work without interruptions and improving operational efficiency.Public Request Portal
Simplify Incoming Maintenance Requests
Incoming maintenance requests from employees and customers can become stressful for your team. If you run a fast-paced company like an energy provider firm, you will likely receive maintenance requests about power outages from field technicians and customers. The public request portal allows users to submit work requests effortlessly. With EZO CMMS, the efficient work order software, you can manage incoming requests and filter them based on priority.Checklists
Ensure Compliance and Quality Checks
Resolving quality control issues can be tough without clear guidelines. This is specifically true for manufacturing companies, where ensuring all safety and compliance is essential before equipment is used. With mandatory checklists, our work order software ensures that your technicians carry out all steps before a work order is marked complete. Detailed and customizable checklists for each task also reduce the risk of errors and maintain consistency for all tasks.Custom Filters
Find the Right Work Orders Quickly
Vendor Management
Improve Collaboration with Vendors
Work Logs
Track Labor Costs With Accuracy
Manage Work Orders, No Matter the Industry
Elevate Your CMMS Experience with
Seamless Integrations
- Help Desk and Service Management
- Identity and Access Management
- Collaboration and File Management
- Advanced Support and CRM
Frequently Asked Questions
Track the completion of maintenance tasks and record the use of resources, including labor and parts with work order scheduling software. For instance, you can track repairs of critical medical equipment in a hospital facility. This data helps maintenance teams plan in an efficient way and improve overall performance.
On-demand, preventive, internal, and third-party are four types of work orders. Urgent repair of a piece of machinery is an example of an on-demand work order whereas a scheduled maintenance task is an example of a preventive work order. You can manage these work orders manually or with an advanced work order management system.
A good example of a work order is repairing a generator belt or fixing a forklift within a manufacturing facility. Work orders are created within maintenance work order software. A work order is a planned task or job that can be assigned to someone, usually a technician. It can be created by your customer or someone from your organization.